Soldering
PL-259 Coax Connectors
Introduction:
My first
experience with the PL-259 coaxial connecter came into my life when I was in my
teens. Like so many others, my two way radio experience was generated through contact
with the use of Citizens Band
radio back in the early 60's. I remember soldering PL-259 connectors
onto RG-8U type coax but for some reason they never quite turned out looking
like the pictures shown in the instruction manuals. Then one day while I was
visiting a friend and HAM at the Navy's instrument calibration lab in Trenton, NJ,
I noticed he was assembling PL-259 connectors onto RG-213U cable. I was amazed
at how precise he was in his installation and how he made up these cables with
ease. As we talked he reveled how at one point in his life with the US Air
Force he sat in a small shack at the end of a runway making up coaxial cables
for radio navigational systems. He also instructed me in the method he used
which I will relay to you here. Over the years I've read all the pro's and
con's of several methods and how the Amphenol method is the only correct way to
install the PL-259 connectors. I've also been told that using a soldering gun
instead of an iron is taboo. All I can say is that this is the method I use and
I'm going to let you decide on the best method you want to use.
Tools that I use:
·
Utility knife
·
1/4 inch square, triangular or flat file
(without handle)
·
Small tubing cutter (nylon preferred)
·
Common pliers
·
Wire cutters
·
Soldering rosin (liquid preferred)
·
Weller 240/260 watt soldering gun (or suitable
iron)
·
A good quality 60/40 solder
·
Volt-ohm meter
·
Petroleum jelly ell or other light lubricant
·
Denatured alcohol (rubbing alcohol)
·
Paper towel or rag
A word about connectors:
There are a
lot of connectors on the market. Some connectors are very well made and some
are pure junk. I prefer to use connectors that don't have a bright shiny
finished on them however a nickel plated shell is fine. These tend to be much
more difficult to solder to.
A word about coax cable:
The method
described here is intended to be used with RG-8, RG-213 type coax constructed
with a solid insulator. It is not recommended to be used with coax constructed
with foam type insulation. While there are many coax cables that are 1/2 inch
in outside diameter, the true size of the cables that interface directly to
PL-259 plugs is 0.405 inches. These instructions will not cover the use of
reducers required for adapting the PL-259 to be used with coax such as RG-8X,
RG-58 or RG-59.
The Process:
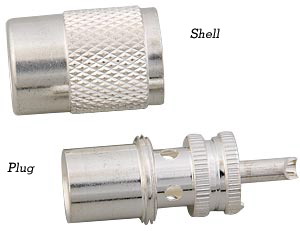
- Start
with preparing the PL-259.
- Remove
the shell from the plug and set aside.
- Using
the handle end of the file insert the tip into each solder hole on the
plug and scrape the edge to remove any debris or plating. You should see
bare brass.
- Next
lay the file flat into the area with the holes and lightly remove any burs
created from cleaning out the holes. At this time you may want to remove
the plating finish around the holes exposing the brass material.
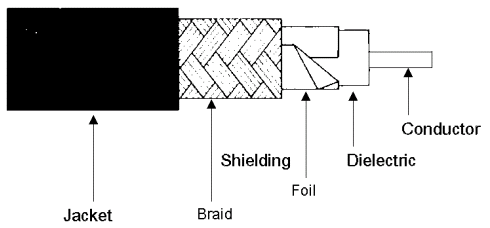
- Next
let's move to the coax and prepare it for accepting the connector.
- Remove
about 2 inches of the coax outer covering known as the jacket. Do this
with a sharp utility knife making sure not to nick the wire braid below it.
The best method I've found using a utility knife is to score the jacket
then bend the coax slightly. This will allow the scored area to split
lessening the chances of nicking the braid below it. This may take a
little patience at first but with practice it will become easier. If you
nick the braid, cut off the coax and start over. Remember, RF travels on
the outside of this braid too. By the way, there are special coax cutters
manufactured specifically for this purpose but they are in the $50 to $100
price range. The choice is yours.
- Apply
one or two drops of rosin on the newly exposed braid close to the jacket.
Use the rosin sparingly and don't overdo it. A little goes a long way. The
purpose of this step is to allow the solder used in the next step to flow
quickly lessening the heat exposure time when applying the solder.
- Using
your soldering gun or iron, apply just enough solder to wick onto the
braid from the jacket toward the end of the coax covering about 1/2 to 3/4
inch all the way around the diameter of the braid.
- Let
the solder and coax cool.
- Using
the tubing cutter, position the outer edge of the tubing cutter housing
against the end of the coax jacket. This should position the cutting wheel
of the tubing cutter the proper distance away from the end of the coax
jacket allowing just enough tinned braid to remain after cutting. Continue
adjusting the cutter deeper as you rotate the cutter. This will cut
through the coax braid and dielectric material. Continue until you have
run out of adjustment with the tubing cutter wheel.
- Remove
the tubing cutter from the coax. You will notice that the cutting wheel
will most likely not reach the center conductor of the coax.
- Take
the utility knife and gently cut into the cut the tubing cutter made. Cut
into the dielectric carefully making sure you do not nick the center
conductor. If you nick the center conductor, cut off your work and start
over.
- Once
you have cut close to the center conductor you can pull on the scrap end
of the coax removing the excess braid, dielectric material exposing the
center conductor. This may have to be accomplished with some force or the
use of pliers on the scrap end. A slight twisting motion in the natural
twist of the center conductor while removing the scrap may also help.
- Now
you should have the coax with about 3/8 inch tinned section exposed along with about 1
1/2 inch of
exposed center conductor. You are now ready to install the PL-259
connector.
- Place
the shell of the connector on the coax in the proper direction. (The
threaded end facing the end of the coax you just prepared). DO NOT FORGET
THIS STEP !!!!
- Apply
a very small amount of lubricant on the jacket. (cover about ¼ inch in
length and all the way around the end of the jacket) This will help
lubricate the plug as it screws over the jacket in the next step.
- Place
the plug of the PL-259 on the end of the coax and screw the plug on until
it bottoms onto the coax. At this point you may want to back the plug off
the coax about 1/8 turn. This will give the coax a little gap between the
dielectric and the insulator inside the plug.
- Looking
through the holes in the connector plug you should see the tinned braid.
Apply enough solder into each hole to ensure a good electrical connection.
Don't get carried away with the heat from the soldering gun or iron. Also
ensure that all holes are completely sealed with solder to help prevent
water from getting into the holes.
- At
this point you may want to lightly try to turn the plug on the coax. If
the plug turns it hasn't been soldered properly and additional solder
needs to be added to each hole.
- Next
check for continuity (a short) between the coax center conductor that
should be protruding out of the connector pin and the body of the
connector plug. You are checking for no continuity (an open) between these
two points. I've deliberately not soldered the center pin prior to making
this first check. This is so it will be easier to remove the connector if
you find a short at this time.
- Next
check for continuity between the body of the plug and the shield at the
opposite end of the coax if possible. You should have a good electrical
connection.
- If all
is well, than solder the center connecter pin to the center conductor of
the coax.
- Clip
off the excess center conductor at the tip of the connector pin and ensure
you have a good solder connection. Add a little more solder to the tip.
- Check
for a short between the center pin and the body of the plug of the
connector. If there is continuity at these two points then you have a
shorted plug and you will have to start over. If you wait to make these
checks after you have installed both connectors, you will not know which
end has the bad connection. You will have a 50/50 chance of being correct
in your guess as to which one is bad so test each connector as you install
them.
- After
all the connectors have been installed and checked for proper continuity,
clean off the excess rosin with the alcohol and screw the shells onto the
connector plugs.
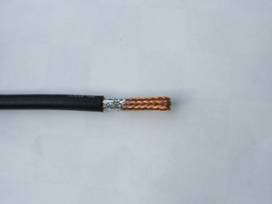
Remove about 2
inches of the
jacket. Tin
about 3/8 inch close
to the jacket.
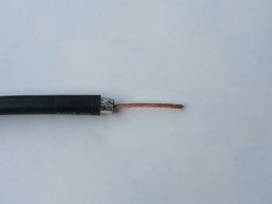
Place the tubing cutter against the jacket. Cut
into the tinned braid/dielectric and remove.
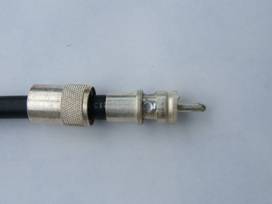
Install the shell then
screw the plug onto the coax. Now solder the plug to the tinned After checking continuity
and plug security, cut off excess center conductor and
braid through the
plug holes. solder
the tip.